ADHESIVES
Today, the most widely used adhesive is One Part Epoxy, which requires heat to cure. Properly cured, it creates a strong bond with all types of surfaces. In order to reduce costs, many flap disc manufacturers use a cheap substitute that is less flexible and has more filler. These adhesives solidify quickly at room temperature, making it difficult to properly position the flaps during manufacturing of a disc.
On the contrary, Extreme Abrasives only uses the highly flexible and top quality One Part Epoxy adhesive that is made in the U.S.A.
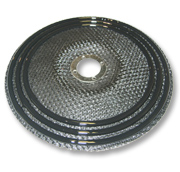
DISC BACKING TYPE
Fiberglass
Advantages |
|
Disadvantages |
|
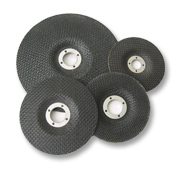
Fiberglass backing is made out of layers of fiberglass mesh bonded and pressed together into a depressed center disc. Generally, 8 layers of fiberglass are used. Many flap disc manufacturers use only 6 or 7 layers in order to reduce costs. This reduces strength and can cause the flap disc to fail. At Extreme Abrasives, we use 8 layers for our 4 ½”, 5”, 6” and 7” discs. For our 4” discs, we use 7 layers since at this size additional layers become redundant. Cost of the backing is also related to density of the fiberglass mesh. Some backing manufacturers use lower density mesh in order to reduce cost. An arbor hole has one or two metal rings which fit the onto the centre nut. A quality backing has layers firmly pressed and the outer diameter grinded concentric to the arbor hole. Due to economies of scale, almost all fiberglass backings are manufactured in China.
Plastic
Advantages |
|
Disadvantages |
|

Plastic backings are mostly made out of nylon. They come in different thickness and hence, cost. Thicker backing is safer backing. Trimming ability is a powerful feature used in marketing, but in reality is way more dangerous than it looks.
Metal
Advantages |
|
Disadvantages |
|
Made from stamped steel or aluminum. Metal needs to be extremely rigid.
I am text block. Click edit button to change this text. Lorem ipsum dolor sit amet, consectetur adipiscing elit. Ut elit tellus, luctus nec ullamcorper mattis, pulvinar dapibus leo.
ABRASIVE MATERIAL
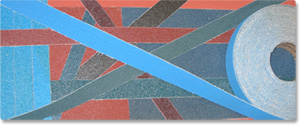
Ignoring the backing and adhesives for a moment, flap disc grinding performance is directly related to the quality of the abrasive material used. Flap disc design can enhance or reduce performance but nothing can replace a quality abrasive material. That is why Extreme Abrasives uses only an abrasive material made by a top European manufacturer.
Main components of an abrasive material are backing, grain and resin.
Abrasive Backing
Backing is one of the most critical components and it is often overlooked. It has to be strong enough to retain grain from wearing too early but not too strong to cause glazing on the surface of the disc. The most widely used are X weight cotton, poly-cotton and polyester backings. Each of these backings has its own advantages and disadvantages. If you would like additional information on how it affects flap disc performance, please don’t hesitate to contact us.
Grain Type
The grain type is dependent on your application. Most common grain used is Zirconium, due to its price to performance ratio and because it works well on all types of metals. We use abrasive material made with Hi-Tech self sharpening zirconium grain. Other commonly used grains are Aluminum Oxide, Ceramic and Silicon Carbide. Lately, non–woven material is also used for finishing discs.
Resin
Resin is used to bond the grain to the abrasive backing. Usually there are two coats of resin but in some cases a third coat is added with agents to improve performance, for cooler grinding and reduced loading and glazing of abrasive surfaces.
PRICE FACTOR: ABRASIVE MATERIAL
Abrasive Material is the most expensive component of a flap disc. That is why many of today’s flap disc manufacturers manipulate the abrasive material in order to offer lower prices than their competition. Customers need to understand the difference between the value and price when making their purchase decision. Here are some examples of how our competitors sacrifice quality in an attempt to manipulate their customers:
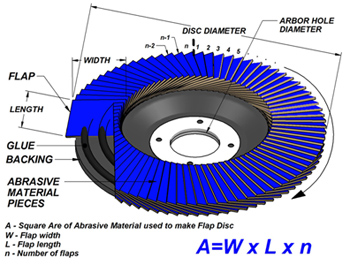
Abrasive Material Quality
Abrasive materials might look and feel the same, but actually using them tells another story. The most visible difference is in coarser grits (36, 40, 50 and sometimes 60 GRIT). The ratio between removed material to disc loss is too low or simply the disc is not performing to its specifications. Quantity of quality grain varies by manufacturer, and so too does the price. There are no performance guarantees; different materials perform identically and sometimes even identical materials perform differently. German manufacturers are leaders in abrasive material manufacturing and they are known for consistent quality. To make sure you are buying the right product, make sure to ask your flap disc supplier about its abrasive material manufacturer and the type of material used. Check with your supplier regularly, as samples could perform differently than product shipments.
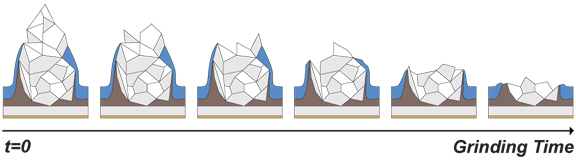
Number of Flaps
Competitor
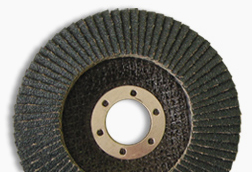
A disc made by the competitor.
Extreme Abrasives
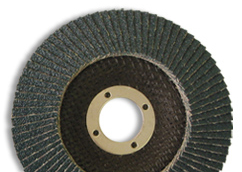
The same disc made by Extreme Abrasives has 80 Flaps.
It is often that flap disc manufacturers offer prices 5-20% lower than their competitors who are using the same material and flap size. You are strongly advised to count the total amount of flaps and establish how much abrasive material is actually used. Without close inspection it is hard to say whether 80 or 75 flaps are used, as evident from the provided photo.
Size of Flaps
Competitor
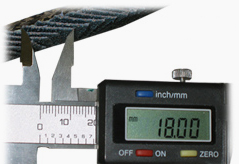
A disc made by the competitor.
Extreme Abrasives
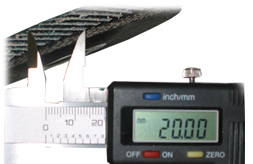
A disc made by Extreme Abrasives.
Competitor
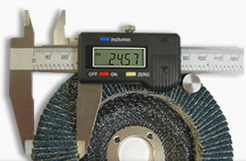
A 5″ disc with 4 1/2″ flap size made by our competitor.
Extreme Abrasives
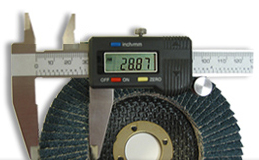
5″ disc with industry flap size, made by Extreme Abrasives.
The best way to determine the amount of material on the disc is to calculate the total surface area of the abrasive material on the disc. Please see the provided formula and compare your results.
Competitor
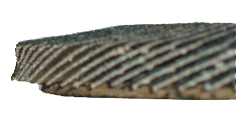
Discs made by our competitors are noticeably smaller/thinner and have less flaps.
Extreme Abrasives
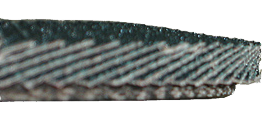
A disc made by Extreme Abrasives does not compromise on materials thus providing thicker discs.
Do not be fooled by disc thickness arguments. Use the above formula to establish the real amount of abrasive material. In the case of equal material used, firmer discs are more aggressive then thinner, while softer discs produce a better finish and are thicker. We recommend that discs are firmer leading to a more aggressive disc which is better during adhesion. The adhesive is squeezed between flaps to create a greater contact area.
ADDITIONAL FACTORS
Disc Balance
For safe and vibration-free operating, it is important that flaps are evenly distributed (equal spacing between flaps) and concentrically placed around the arbor hole. It is equally important that the adhesive is distributed evenly, concentrically and positioned to cover the largest area under the flaps. Today there are many flap disc manufacturers that use fully automatic equipment. Due to the nature of abrasives and the changing viscosity of adhesives, it is often that flap discs are created without proper balance. Extreme Abrasives ensures that all discs are inspected prior to shipping.
Flap appearance
In many cases, flaps have fibers sticking out as result of the abrasive material slitting or cutting. The coarser the grit, the more obvious it is. This should be treated as a cosmetic issue which does not affect disc performance.
Packaging
The way flap discs are packaged can make a big difference in the total shipping costs to the customer. Consider packaging which is focused on the market you are trying to target.